The Science Behind Porosity: A Comprehensive Overview for Welders and Fabricators
Recognizing the elaborate systems behind porosity in welding is vital for welders and fabricators pursuing remarkable workmanship. As metalworkers explore the midsts of this sensation, they reveal a world governed by numerous elements that influence the development of these tiny spaces within welds. From the make-up of the base materials to the complexities of the welding procedure itself, a wide variety of variables conspire to either aggravate or alleviate the presence of porosity. In this thorough overview, we will untangle the science behind porosity, discovering its effects on weld top quality and unveiling progressed strategies for its control. Join us on this journey with the microcosm of welding flaws, where accuracy meets understanding in the quest of flawless welds.
Understanding Porosity in Welding
FIRST SENTENCE:
Evaluation of porosity in welding discloses vital insights into the stability and quality of the weld joint. Porosity, identified by the presence of tooth cavities or gaps within the weld metal, is a common worry in welding processes. These spaces, otherwise appropriately addressed, can jeopardize the architectural stability and mechanical residential or commercial properties of the weld, leading to potential failings in the finished product.

To discover and measure porosity, non-destructive testing techniques such as ultrasonic testing or X-ray examination are frequently used. These strategies allow for the identification of interior flaws without endangering the stability of the weld. By evaluating the dimension, form, and distribution of porosity within a weld, welders can make educated decisions to enhance their welding procedures and attain sounder weld joints.

Variables Affecting Porosity Development
The event of porosity in welding is influenced by a myriad of factors, varying from gas securing efficiency to the complexities of welding specification setups. One important variable contributing to porosity development is inadequate gas shielding. When the shielding gas, generally argon or CO2, is not properly covering the weld pool, atmospheric gases like oxygen and nitrogen can infect the liquified metal, leading to porosity. Furthermore, the tidiness of the base products plays a significant function. Pollutants such as rust, oil, or moisture can evaporate during welding, developing gas pockets within the weld. Welding criteria, consisting of voltage, existing, take a trip speed, and electrode kind, likewise impact porosity development. Making use of improper setups can produce too much spatter or warm input, which consequently can lead to porosity. The welding strategy employed, such as gas metal arc welding (GMAW) or secured steel arc welding (SMAW), can affect porosity formation due to variants in warm distribution and gas protection. Comprehending and regulating these elements are essential for minimizing porosity in welding procedures.
Effects of Porosity on Weld Top Quality
Porosity formation substantially compromises the architectural integrity and mechanical residential properties of bonded joints. When porosity is existing in a weld, it creates gaps or cavities within the material, decreasing the total stamina of the joint. These voids function as stress focus points, making the weld more at risk to cracking and failure under tons. The presence of porosity additionally weakens the Your Domain Name weld's resistance to deterioration, as the caught air or gases within the gaps can respond with the surrounding atmosphere, causing destruction gradually. In addition, porosity can hinder the weld's ability to hold up against pressure or influence, additional jeopardizing the general quality and integrity of the bonded structure. In crucial applications such as aerospace, vehicle, or architectural building and constructions, where safety and resilience are critical, the destructive results of porosity on weld top quality can have severe effects, emphasizing the value of lessening porosity with proper welding techniques and procedures.
Techniques to Reduce Porosity
To boost the quality of bonded joints and guarantee architectural integrity, welders and fabricators employ specific methods aimed at reducing the formation of voids and tooth cavities within the product throughout the welding process. One efficient technique to lessen porosity is to ensure correct material prep work. This includes extensive cleansing of the base steel to get rid of any impurities such as oil, oil, or moisture that can contribute to porosity formation. Furthermore, using the appropriate welding parameters, such as the proper voltage, current, and take a trip speed, is crucial in preventing porosity. Maintaining a constant arc length and angle during welding additionally assists minimize the chance of porosity.

In addition, picking the appropriate shielding gas and maintaining proper gas flow rates are essential in minimizing porosity. Utilizing the proper welding method, official source such as back-stepping or utilizing a weaving activity, can additionally aid disperse heat equally and decrease the opportunities of porosity development. Making sure proper air flow in the welding atmosphere to get rid of any type of potential resources of contamination is important for achieving porosity-free welds. By executing these strategies, welders can efficiently reduce porosity and produce premium welded joints.
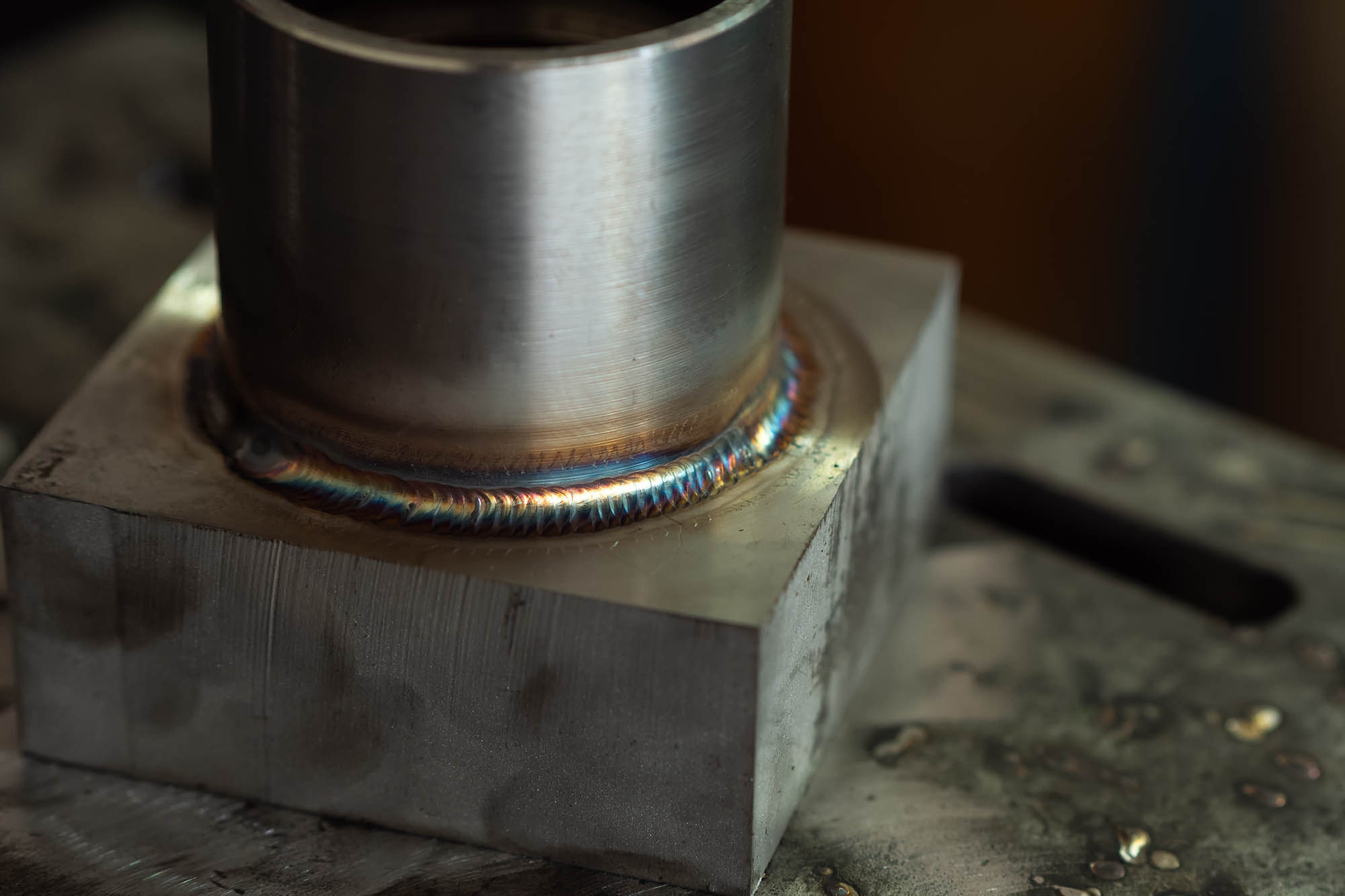
Advanced Solutions for Porosity Control
Implementing advanced technologies and ingenious approaches plays an essential duty in achieving superior control over porosity in welding procedures. Additionally, using advanced welding techniques such as pulsed MIG welding or modified ambience welding can also aid minimize porosity issues.
One more sophisticated service involves the use of sophisticated welding equipment. For instance, utilizing equipment with integrated attributes like waveform control and advanced source of power can enhance weld quality and decrease porosity risks. The execution of automated welding systems with exact control over parameters can dramatically minimize porosity defects.
Additionally, incorporating sophisticated surveillance and inspection modern technologies such as real-time X-ray imaging or automated ultrasonic testing can assist in finding porosity early in the welding process, enabling prompt rehabilitative activities. Generally, integrating these innovative options can considerably improve porosity control and enhance the overall top quality of welded components.
Final Thought
In conclusion, comprehending the see this website science behind porosity in welding is vital for welders and makers to produce top quality welds - What is Porosity. Advanced options for porosity control can further improve the welding procedure and make sure a solid and dependable weld.
Comments on “What is Porosity in Welding: Secret Factors and Their Effect On Weld Quality”